- 「ウェッジベースランプ(自動車用小型電球)」 世界シェア40%
- 「液晶バックライト用冷陰極放電灯」 世界シェア60%
【会社概要】
本社所在地 | 今治市旭町5-2-1 |
---|---|
創 業 | 1944年10月 |
資本金 | 41億1千万円 |
代表者 | 小林 久夫![]() |
【会社沿革】
1944年 | 創立 東芝今治工場 |
---|---|
1950年 | ハリソン電機(株)設立 |
1965年 | ウェッジベースランプの生産開始 |
1986年 | 冷陰極放電灯の生産開始 |
2000年 | 東芝ライテックの産業機器部門と一体化し社名変更 |
2002年 | 今治に第4番目の工場棟新設 |
長引く不況と産業空洞化の進展などにより苦戦を強いられている日本の製造業。愛媛のモノづくりも全国同様、大変厳しい局面に立たされている。しかしながら県内には、このような厳しい状況下にあっても、世界一または日本一のシェアを誇る製品を持ち発展を続けているメーカーも数多くある。
そこで今回よりシリーズとして、特定分野で世界一あるいは日本一のシェアを持つ県内事業所を“クローズアップ”し、なぜ世界一あるいは日本一になったのか、どのようにしてそのトップの座を維持しているのか、などの秘密を明らかにしていくこととしたい。
第1回目は、自動車用小型電球(ウェッジベースランプ)、液晶バックライト用光源(冷陰極放電灯)で世界一のシェアを持つハリソン東芝ライティング(株)を紹介する。
1.「ウェッジベースランプ」世界シェア40%
~自動車の超小型電球~
皆さんは自動車一台にどのくらいの電球が使われているかご存知だろうか? 自動車用の電球といえば、ヘッドライト、ブレーキランプ、室内灯などが真っ先に思い浮かぶだろうが、その他にもスピードメーターやエアコン、カーステレオなどが収まるダッシュボード周辺にも数多く使われている。車に乗ってエンジンをかけると、目の前のダッシュボードからグリーンやブルーなどの鮮やかな光が視界に飛び込んでくる。ダッシュボードのメーター類やオーディオ機器の中にたくさん取り付けられている“直径が5~20mm”の小型電球こそが同社の主力製品の一つである「ウェッジベースランプ」である。通常、車一台当たり大衆車で約30球、高級車では約60球もの電球が使われているが、その大部分を“小型電球”が占めている。
「ウェッジベースランプ」は、差込口が楔(くさび)の形をしているため、 “楔型(くさびがた)電球”とも呼ばれている「口金なし小型電球」である。ねじ切り式の口金がある家庭用電球と異なり、ソケット付きの基板に“カチッカチッ”と簡単に取り付け取り外しができる点に特徴がある。
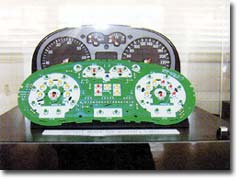
自動車のダッシュボードに取り付けられた
「ウェッジベースランプ」(使用例)
~マイカーブームの波に乗る~
元々、家庭用電球メーカーだった同社が、「ウェッジベースランプ」の生産を開始したのは1965年であり、他社に先駆けてのスタートであった。その後、“マイカーブーム到来”とともに、従来の「口金あり電球」より小型・軽量で価格が安く、しかも取り付け取り外しが容易な「ウェッジベースランプ」の需要が急速に高まり、同社の生産量は右肩上がりに増加した。「生産が間に合わず、自動車の生産ラインに支障を与えるほど需要があった」と取締役自動車光源事業部長の真部氏は当時を振り返る。さらに、82年からは輸出を開始、北米ビッグ3をはじめとする海外自動車及び自動車関連メーカーとの新規取引に成功し、瞬く間に世界のトップシェアを獲得するに至った。同社の今日の発展の第一歩は、自動車産業の成長を見抜き、他社に先駆け市場に参入を決断したことにある。
~通算100億個達成~
低価格戦略で同社を追撃しようとする後発メーカーがこれまでに何社もあったが、“高品質かつ安定した供給能力を持つ” 同社に対する顧客の信頼は微動だにしなかった。93年11月には通算50億個、今年1月には同100億個を達成し、今や“国内シェア80%、世界シェア40%”を誇っている。ただ、ここ2、3年は、スピードメーターなどの自動車用光源として「LED(発光ダイオード)」の需要が伸びており、「LED」との競合が強まっている。このため、小型電球の生産に加え、新たな顧客ニーズにも対応できるよう今年5月からは「LED」の生産も開始した。
2.「液晶バックライト用冷陰極放電灯」世界シェア60%
~液晶の光の源~
「冷陰極放電灯」とは、パソコン等の液晶パネルの背面に取り付けられた“液晶用バックライトユニット”の光源として用いられる細い蛍光灯のことである。液晶モニターは「2枚のガラス板の間に液晶を挟み込み、通電することで液晶分子の並び方をコントロールし、画面に光を通したり通さなかったりする部分をつくり出す」ことで画像が浮かび出る。したがって、バックライトなくしてはディスプレイとして機能しない。つまり、「冷陰極放電灯」は液晶ディスプレイにとって欠かすことのできない要素部品と言え、まさに液晶の光の源なのである。
液晶ディスプレイは、ノートパソコンをはじめとして、モニター、携帯電話などの画面として幅広く使われており、高い成長性を誇っている。最近では、15インチ以上の大型モニター用及びテレビ用の需要が拡大中であり、この1年間で液晶モニターの市場規模は55%以上伸びると予想され、「液晶バックライト用冷陰極放電灯」の需要も今後ますます拡大する見通しである。
「冷陰極放電灯」は、液晶ディスプレイ用をはじめとして、FAXの読取り光源や複写機のイレーサー光源などに幅広く使われているが、液晶ディスプレイ用としての使用が急速に拡大している。
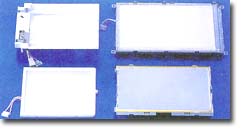
「冷陰極放電灯」を使用した液晶用バックライトユニット
同社が「冷陰極放電灯」の製造を開始したのは84年である。参入当時は主力の「ウェッジベースランプ」が右肩上がりで成長している真っ最中であったが、同社は将来の液晶ディスプレイの発展を見越して参入を決断したとのことである。「冷陰極放電灯」は、他社より先発であった「ウェッジベースランプ」の場合とは異なり、国内でも3、4番目の参入と後発であったが、先行メーカーを凌ぐペースで軽量小型化や光力アップなどの新技術の開発に成功するとともに、高品質製品を供給し、短期間で世界シェア60%を占めるに至った。
最近、ノートパソコンの薄型化が進むなど、「冷陰極放電灯」の軽量小型化ニーズが一段と高まっているが、約10年前には “直径8 mm”が最小サイズだった「冷陰極放電灯」を、同社ではなんと“直径1.6 mm”までの細管化に成功している。また、製品の寿命性能についても、それまで通常8千時間程度であったものを、現在では最長“7万時間”にまで長寿命化させ、ライバル企業に対する優位性を保っている。さらに、鉛ガラスから鉛レスの半硬質ガラスへの転換など環境面に配慮した製品を、他社に先駆けて積極的に市場に投入している。このような他社より常に一歩先を行く新製品開発が他社の追随を許さない強みなのであろう。
3.世界一、日本一になった秘密に迫る
~的確な“選択と集中”~
同社が世界トップになった要因の一つは、モータリゼーションあるいはIT革命といった時代の大きな波に乗り成長を遂げた“自動車”あるいは“液晶ディスプレイ”というマーケットを確かな眼で“選択”し参入を果たしたこと、そして限られた“ヒト・モノ・カネ”を戦略商品に“集中”して投入してきたことであろう。
「ウェッジベースランプ」の場合、競合他社より早い時期に経営資源を集中的に投下、量産体制をいち早く整備し、独占的に事業をスタートさせた。この思い切った“選択と集中”の戦略は「冷陰極放電灯」にも生かされている。「ウェッジベースランプの“成功のDNA”を冷陰極放電灯に全て注ぎ込んだ」と取締役放電灯事業部長の渡辺氏は語る。「冷陰極放電灯という花が咲いている間に、次の種を蒔く必要がある」との戦略的な考え方から、同社ではすでに次の主力製品の開発にも取り組んでいる。
~製造ラインも自社でつくる~
同社の強みの一つに、製造ラインを自前で設計・製作する能力がある。「専門機械メーカーに発注すれば完成まで2年程度はかかるが、自社でつくれば半年でできる」と渡辺氏が語るように、投資コスト削減はもとより、製品のライフサイクルがますます短縮化される中、スピーディーな新製品開発と量産体制の確立で市場ニーズへの迅速な対応を実現している。また、机上ではなく現場の声に裏打ちされて自前で作った機械であるため、トラブルが起きた場合でも短期間での解決が可能という。新商品でも、半年経てば次の新商品に追い抜かれるといわれるほど競争が激しい業界において、トップの座を維持し続けている秘訣は、「新製品開発」「設備ラインの設計・製作」「量産化」を三位一体(さんみいったい)でスピーディーに進める体制ができていることにある。
~トップの姿勢が品質レベルを決める~
「トップシェアを勝ち得るためには、価格の安さだけではダメ。高品質の製品を安定して供給できるかどうかに尽きる」と真部氏は語る。
ランプ類の製造では工程中に数箇所のチェックポイントを設け、最新の画像処理技術を駆使した検査システムを導入している。それによってラインから出てくる製品は全て品質が保証される。さらに全数検査を実施することで万全のチェック体制を確立、超小型の製品を大量生産しながら高品質を維持するという極めて困難な問題を解決している。今や100万個に1個の不良品も出さないレベルに達しているそうだ。
この徹底した品質へのこだわりは、「今から20数年前に、当時としては非常に高額な自動検査機の導入をトップが決断したことが契機になった」と真部氏は語る。すなわち、自動検査機導入の決断を行ったトップの高品質追求の強い思いが、社内全体に浸透したのだという。高度化した検査機械やシステムの導入もさることながら、従業員の品質に対する高い意識が、現在の安定した高品質を実現しているといってよいだろう。
お客様に鍛えられた品質管理
「かなり以前に不良品が発生した際、同社は電子顕微鏡で1,000枚もの写真を撮って原因を解明した。その分析結果を説明に出向いたところ、驚くことに納入先の企業でも、同社と同じ様な原因究明のための作業を行っていた。双方の分析結果をつき合わせると同じ結果が出ており、このことを契機にお互いの信頼関係はさらに厚くなり、2度と不良品を出さない体制づくりにつながった。
品質に厳しい顧客と一体となって不具合対策とその定着に当たった結果が、現在の鉄壁の品質管理に繋がっている。真部氏は語る、「厳しいお客様に鍛えられて品質管理面の向上が図られた。厳しいお客様こそありがたいお客様だ」と。
~ハリソン版「プロジェクトX」~
「一つのことを真面目にとことんやる」という今治人気質もまた同社のモノづくりを支えている。「ウェッジベースランプ」の需要が伸び続けていた時代には、「生産が注文に追いつかず、社員の奥さん達も内職を引き受け、増産に協力した」といわれている。不具合が発生したときには、徹夜してでも必ず解決するといった熱意を持った従業員が多い。同社では「プロジェクトX」のような血と汗と涙の人間ドラマがこれまで幾つも繰り広げられてきたという。
4.さらなる飛躍を目指して
~今治に最新鋭工場を建設~
今年3月、需要が急拡大する「冷陰極放電灯」を増産するため、今治に最新鋭工場を稼動。他社の3倍強もの量産体制を確立させ、トップメーカーとしての地位を磐石なものにしている。製造業の多くがアジアに生産拠点を移す中、同社はなぜ今治に新工場を建設したのだろうか。「「冷陰極放電灯」は、今後も成長が見込まれる製品だけに熾烈な製品開発競争が繰り広げられており、開発のスピードが命運を分けるといわれている。そのため、高品質・高水準なモノづくりをスピーディーに行うことが可能な “お膝元の今治”での工場増設を決意した」(渡辺氏)のである。
製造業の空洞化により雇用面を中心に大きな影響が続いている現在、同社の今治での工場増設は地元にとって久々の明るいニュースであった。もちろん同社も、ハロゲンランプやサブミニチュアランプなど製品の一部は既に海外生産に移行済である。しかし「高付加価値品は国内生産」という経営方針を貫き、24時間操業・年中無休・オール自動化という国内生産体制で海外生産品に対抗し、世界のトップメーカーの座に君臨する同社こそ、21世紀の日本の製造業が目指すべき姿ではないだろうか。
~ERP導入!変革の手を一時も緩めず~
同社は経営の効率化をさらに進めるため「ERP(Enterprise Resource Planning)」を、今年3月、全社に導入した。「ERP」とは、企業内でセクション毎に個別管理されていた、財務・人事・生産・物流などの情報を総合的に管理するための手法である。同社の全ての業務の流れを紙に書いてみる(IE分析)と、ERP導入前の用紙の長さは約75mになっていたが、導入後は25mまで短縮できたという。その改善効果は極めて大きいようだ。
導入に必要な「ERPパッケージ」と呼ばれるコンピューターのソフトウェアにはオランダ製の「BAAN」を採用した。「ERP」を導入する場合、現状の仕事のやり方に合うようにソフトウェアをカスタマイズ(修正)する企業が多い中、「企業文化・企業風土の変革」と「人の成長」を導入の狙いとした同社はノンカスタマイズ(無修正)を貫き、「仕事の仕組み」「仕事のやり方」を変えていった。いわば「足に靴を合わせるのではなく、靴に足を合わせることでしか抜本的な変革はできないとの信念を貫いた」(渡辺氏)のである。導入後、リードタイムの3割短縮、部品在庫の3割削減などの成果を上げ、顧客満足の向上により競合メーカーとの差をさらに広げようとしている。
「立ち止まることなく、絶えず走り続けなければならない。気を抜いた途端、トップの座から滑り落ちてしまう」。同社は世界トップの座に安住することなく、危機感を社員全員が共有し、積極果敢な挑戦を続けている。「選択と集中」「三位一体の製品供給」「高品質の徹底追求」を実行し、トップ企業の道を歩む「ハリソン東芝ライティング株式会社」。今後も、愛媛の“世界一企業”の1社として益々の躍進を期待したい。
最後に小林久夫社長が、同社の若い研究者たちに語りかけた情熱的な言葉で締めくくりたい。
「大胆な発想で緻密に考え、夢に見るほど悩むことが必要だ。夢に出るようになれば、必ず解決の光が見えてくる。」
(二宮 秀介)
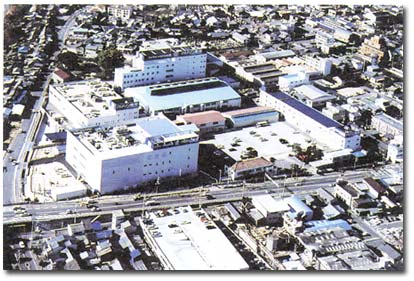
本社全景